Is it possible for alternative fuels to replace traditional fossil fuels as the mainstream?
If you were a coal-burning company, would
you like to choose $60 alternative fuels per ton or $180 coal fuels per ton?
Of course, such a direct comparison is not
reasonable because alternative fuels differ from coal in terms of calorific
value of combustion and disposal costs. Let us then calculate the actual
economic benefits of alternative fuels compared to fossil fuels (as represented
by coal) when the carbon reduction benefits are set aside.
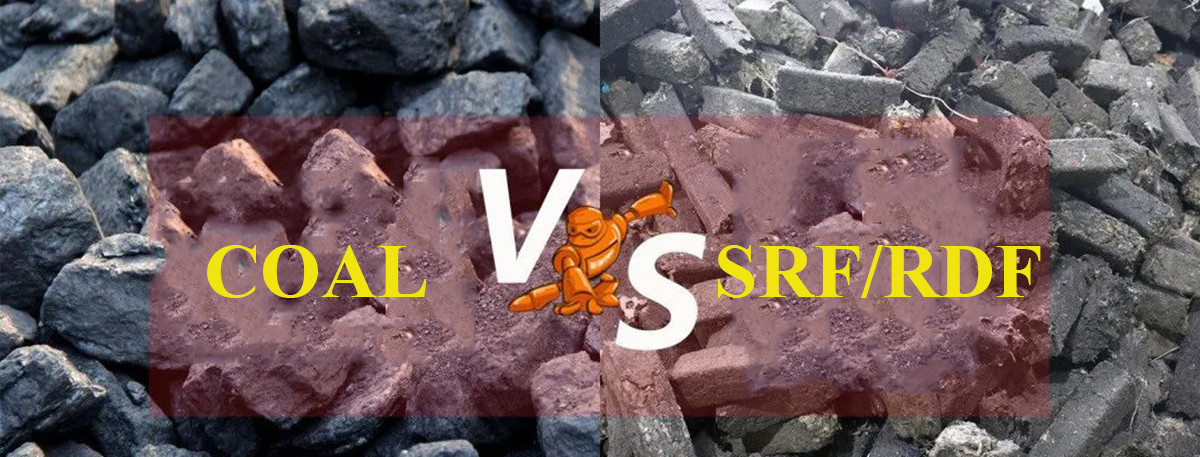
The essence of fuel is to provide heat.
Many places in the industry now already use the price per unit of calorific
value of fuel to calculate, which is much more scientific!
(30-17.5)/30=42.7%.
Heat Loss Coefficient Ratio
Alternative fuels made from different
solid waste materials and different preparation technologies have very
different heat loss and burn-up rates compared to coal, which can be calculated
together as a heat loss factor ratio, generally 1.15. Some high-quality alternative
fuels can achieve less than 1, which is even better than coal (e.g. alternative
fuels made from waste tires).
Pre-treatment Costs
There are labor costs and equipment costs
associated with the preparation of alternative fuels, and the cost of these
pre-treatments is around 10%.
The actual 1000 calorie alternative fuel
would then be $17.5 x (heat loss factor ratio 1.15 + treatment cost 0.1) which
equals approximately $22.
At this point, the difference in benefits
of alternative fuels compared to coal is only 26%.
Although the above calculations are ideal,
they also show that the economic benefits of alternative fuels can be improved
by using better alternative fuel preparation technology and reducing the heat
loss coefficient ratio, which can significantly increase the average calorific
value of the alternative fuel.
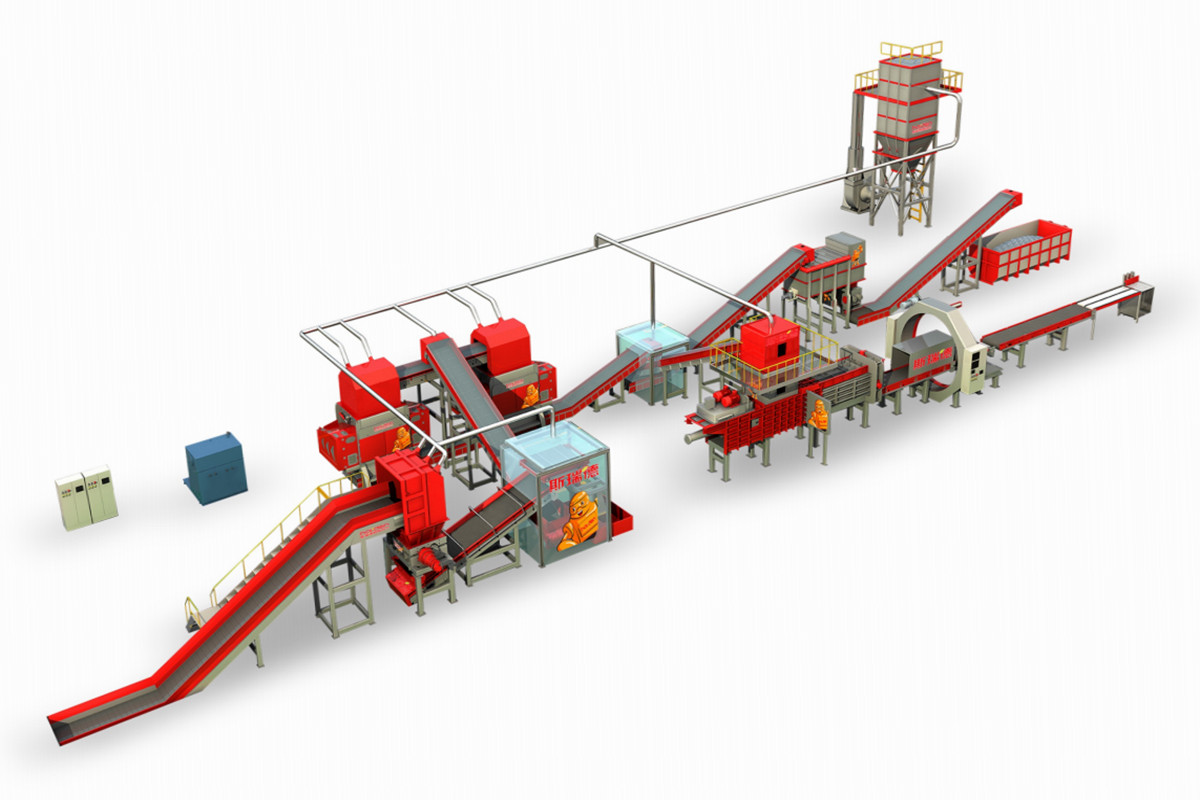
Alternative fuel preparation system for
solid waste
Harden has studied the solid waste
treatment industry in depth for more than ten years and has a total solution
for solid recovered fuel (SRF) and refuse-derived fuel (RDF) preparation in the
fields of municipal solid waste (MSW), bulky waste, paper mill waste, biomass waste,
industrial solid waste, waste tires, agricultural and forestry waste, etc.
By integrating advanced solid waste
shredding technology concepts and relying on the strength of continuous
innovation in independent research and development, Harden's solid recovered
fuels are better in terms of material size and impurity removal rate, with a
lower heat loss coefficient and an average combustion calorific value of
4,800-5,200 calories through the process of secondary shredding, magnetic
separation, air separation, sorting, dust removal and granulation.
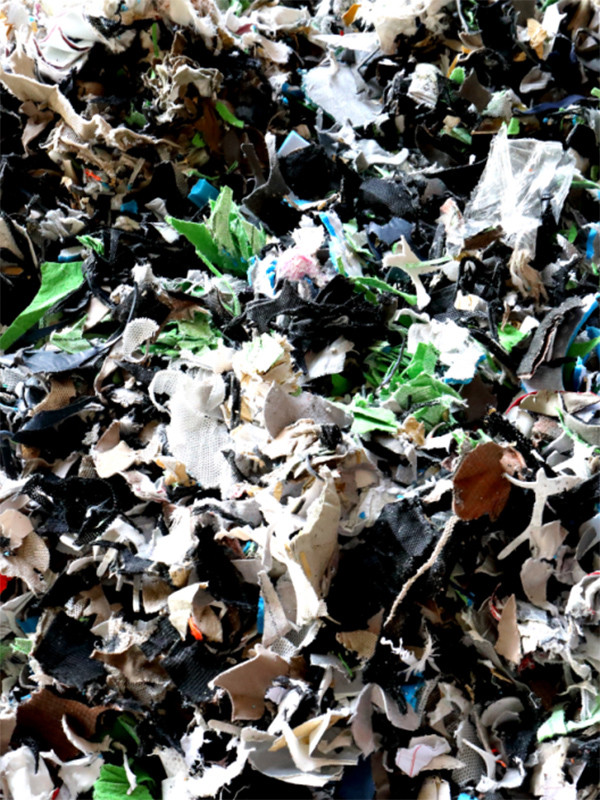
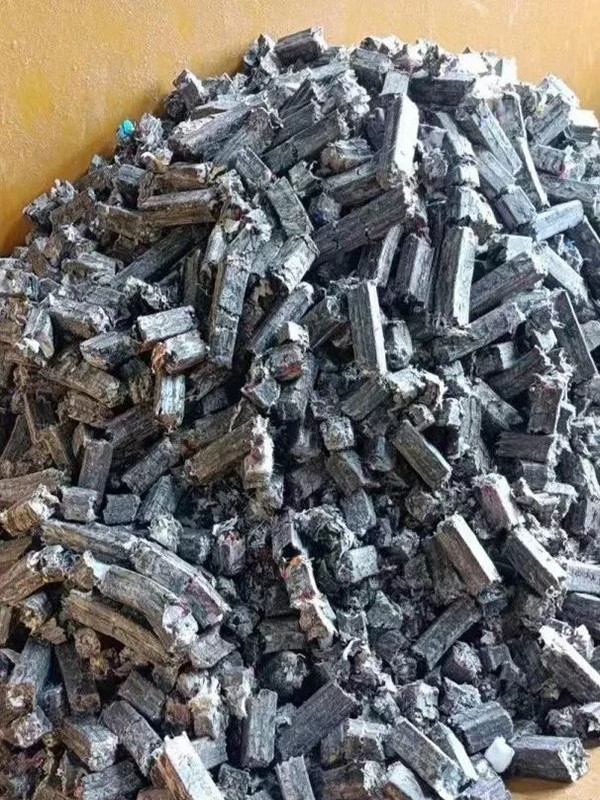
The main factors affecting the calorific
value of combustion of alternative fuels are moisture content and discharge size.
1) Moisture
content: Most alternative fuels have a moisture content of around 15%; The
alternative fuels produced by Harden's alternative fuel technology contain less
than 5% water. (Alternative fuels made from different materials can vary
greatly in moisture content.)
2) Discharge
size: Most alternative fuels are available in the mm level; whereas Harden divides
the discharge size level into 30mm below, 50mm below, 80mm below and 120mm
below according to the modular combination of different processes and according
to the customer's needs, which is more user-friendly.
Selected Cases of SRF/RDF Preparation
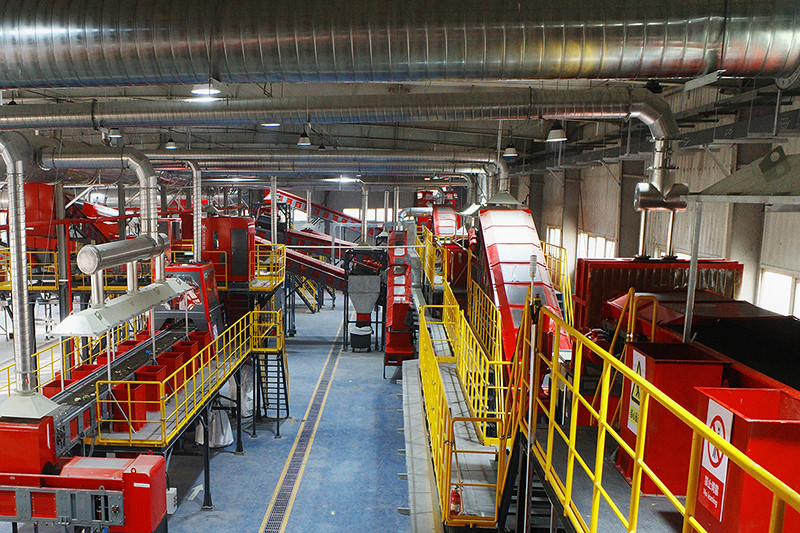
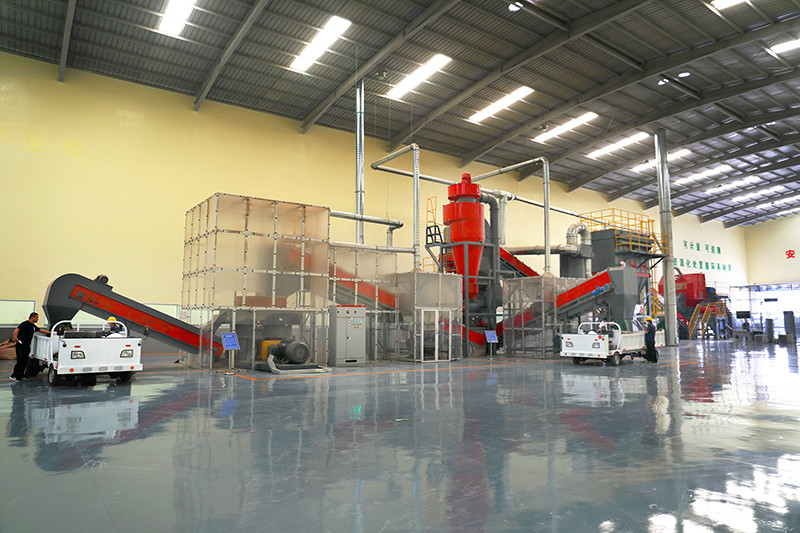
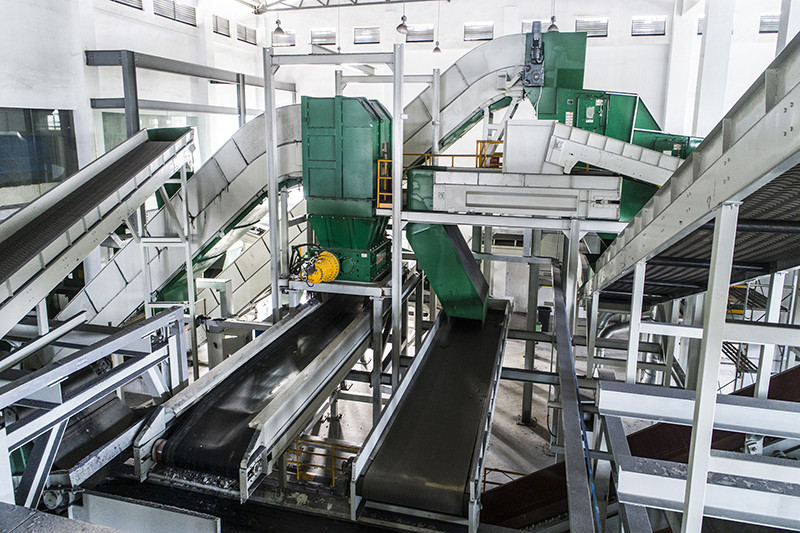
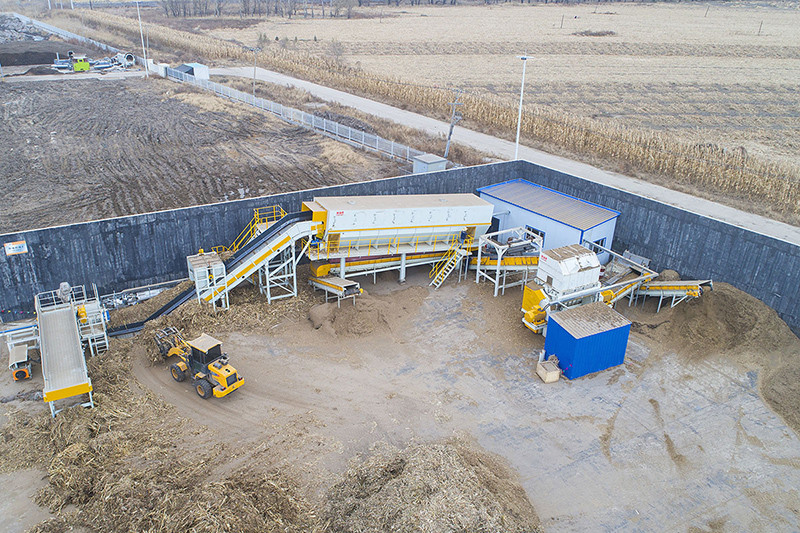
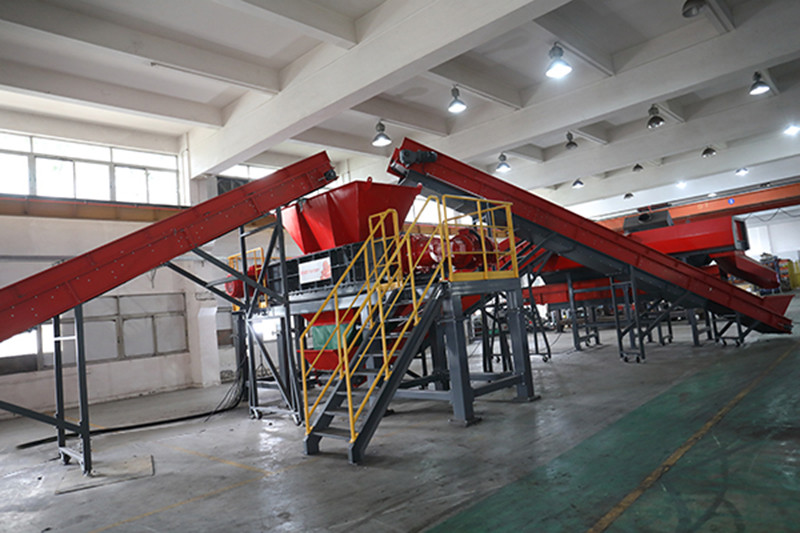
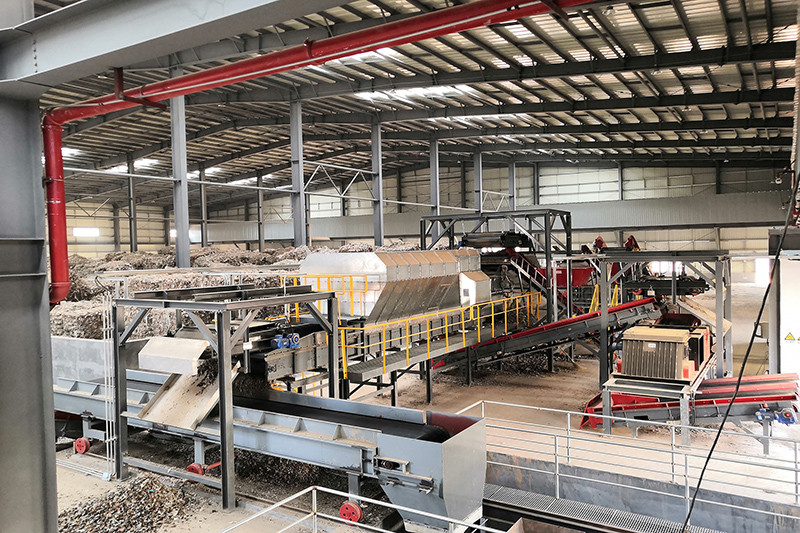
In the context of global carbon emission
reduction, all industries are promoting a low-carbon and environmentally
friendly green economy, and one of them is Harden’s SRF/RDF preparation
technology. It can be used to process industrial waste from daily life and
industrial production, and then through an integrated process and continuous innovative
research and development, it can be used to produce better SRF/RDF fuels to
gradually replace the use of fossil fuels and achieve a new ecology of carbon
reduction and economic benefits.
Video