How does this solid recovered fuel (SRF) preparation system save millions
Cement
is a traditional industry with high energy consumption. Fuel and power costs account for over 50% of cement production costs. Because coal prices have
nearly tripled since 2021, the fuel costs for cement plants have also increased,
forcing the industry to raise cement prices to maintain profits.
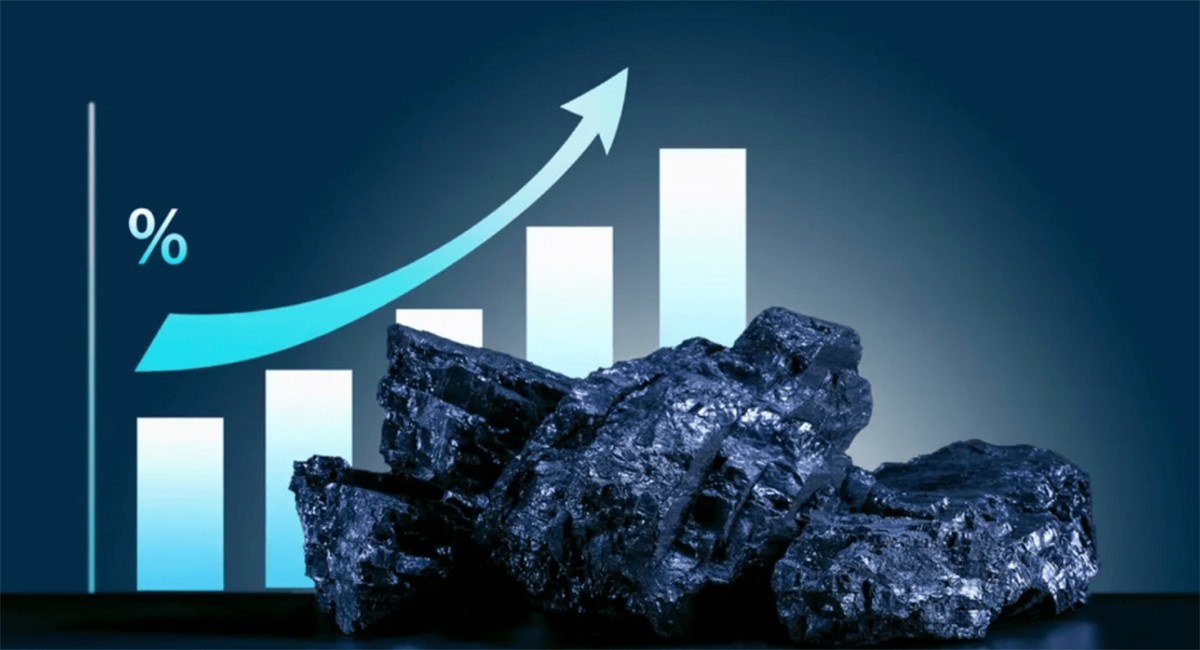
One
cement plant client used the SRF preparation system for industrial solid waste
developed by Harden, to maintain its fuel costs even as coal prices rose.
Operational in 2022, the system has produced 40,000 tons of SRF for the cement
plant, saving nearly $5 million in coal costs.
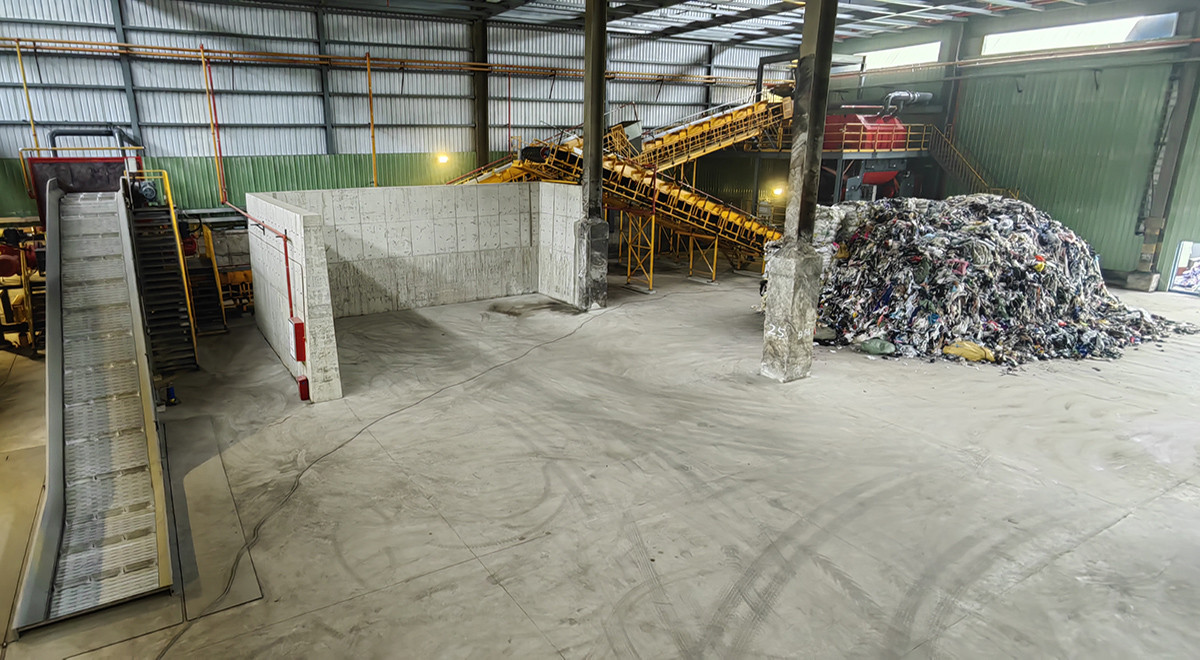
The
system uses dual-stage shredding, magnetic separation, dust removal and other
processes to prepare industrial solid waste into SRF with discharge size less
than 100mm, a production capacity of 15 tons per hour, shredding qualified rate
of more than 95%, and thermal replacement rate is about 70%, which meets the
basic needs of coal burning in cement kilns.
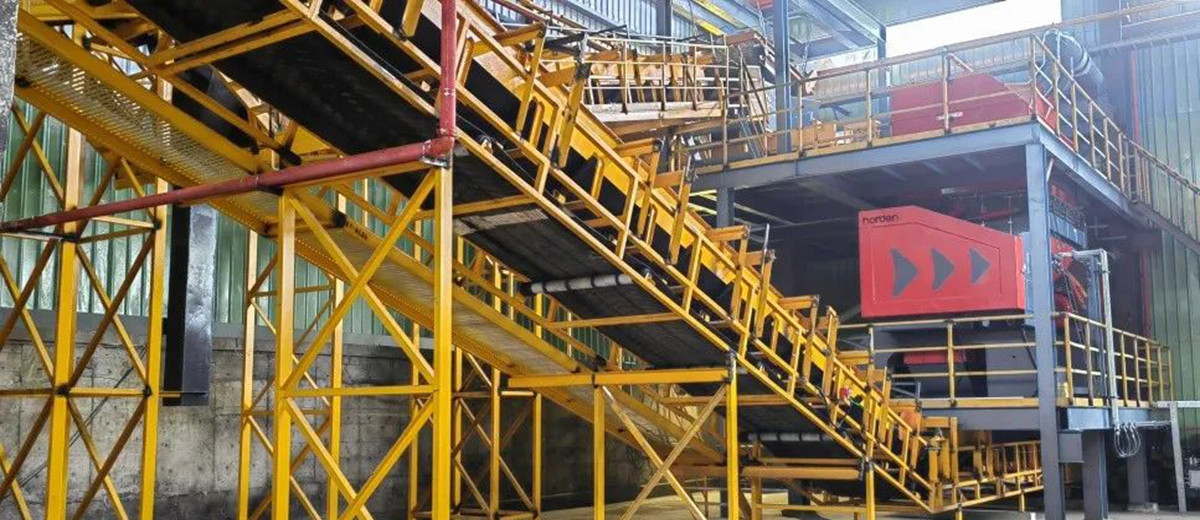
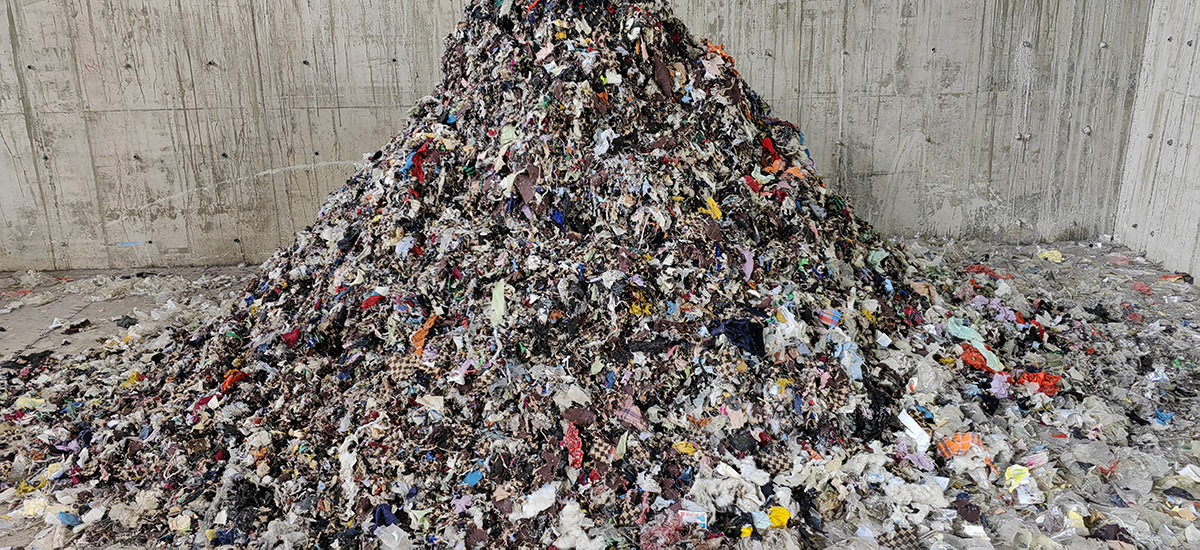
In
the context of global carbon emission reduction, it is very important to
promote green low-carbon circular economy, and how to do this is also a problem
that cement enterprises have to consider. The SRF preparation system can not only make resource utilization
of industrial solid waste generated in daily life and industrial production,
improve resource utilization efficiency and reduce environmental pollution, but also reduces the cost of coal burning for enterprises and greatly
improves the revenue and profit, which will be the only way for the future
development of the cement industry to reduce coal, energy conservation and
carbon emission reduction.